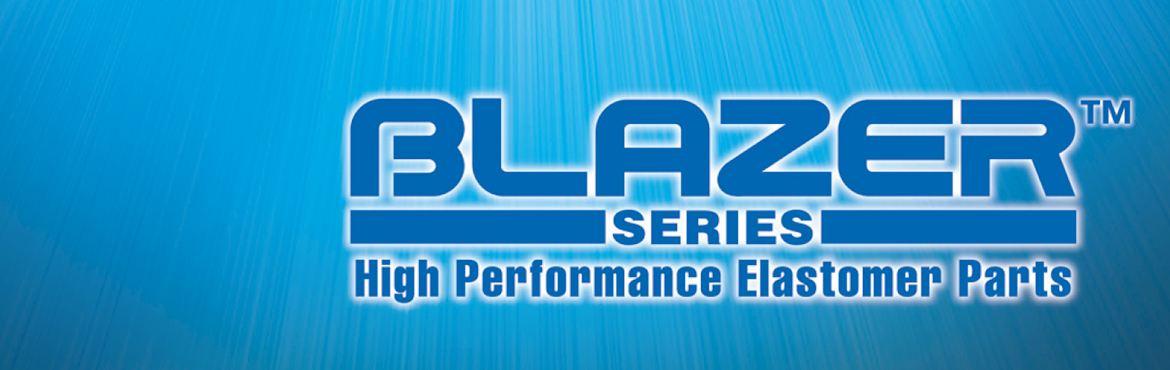
BLAZER™ comparison - Part 3.
O-rings are widely used in a variety of industries. Their required resistance covers anything from chemical to rapid gas decompression and more. As such, there are countless types of O-rings available.
Using patented cross-linking technology, NICHIAS has developed an O-ring series called BLAZER™ for highly specific and high performing applications. These are widely used in Asia but now made available for customers in Europe with highly demanding applications.
These applications can be grouped into 3 main categories – Chemical and/or Plasma; Heat and/or Steam; Rapid Gas Decompression.
Our technical team has put together an overview of the Rapid Gas Decompression environments, its challenges and appropriate solutions.
RGD resistance
O-rings used in oil and gas field plants, infrastructure using steam, power plant, downhole and surface equipment are likely going to be exposed to Rapid Gas Decompression (RGD). Out of all operating environments (chemical, plasma, heat or steam), RGD has effects that may be least noticeable since they happen on the inside of the O-ring and are uncovered only after fatal failure. Cracks that appear in the material can only be discovered by analysing cross-sections of the O-ring. Once the O-ring cracks on the outer surface it is already too late.
Cracks on the inside of the material are caused by highly compressed gas entering the structure of the O-ring and when this gas decompresses rapidly, it expands within the O-ring at an accelerated rate, tearing the material, which in turn affects the products sealing ability.
There are only a few product options on the market provided by DuPont and Greene Tweed, and any material anyway needs to pass International and European standards such as the recognized testing method for North Sea – NORSOK.
BLAZER™ is comparable to Kalrez™ and Chemraz™ solutions (and is also NORSOK certified).
When BLAZER™ is used in combined environment of 300°C steam and RGD, there appear no cracks on the cross-section of the material. It can also withstand multiple cycles of gas compression-high pressure maintenance-RGD-normal pressure-gas compression.
As the most recently developed and certified solution on the market, BLAZER™ G is an appropriate and suitable replacement for other materials currently available.
Comparison chart based on internal test data:
|
BLAZER™ |
Kalrez™ |
Chemraz™ |
Rapid Gas Decompression |
✓ |
✓ |
✓ |
Steam resistance |
✓ |
✘ |
✘ |
Crack resistance |
✓ |
✓ |
✓ |
Compression set |
✓ |
✘ |
✘ |
Chemical resistance* |
✓ |
✓ |
✓ |
*for a full list, please enquire
Applicable BLAZER™ products:
TOMBO No. – BLAZER™ G
Appropriate replacement for:
Kalrez™ 0090, 3018
Chemraz™ 526
Difference in performance and applicability of FKM and FFKM material when it comes to plasma resisti…
Read moreImproved EPDM material application as heat exchanger gasket
Read moreNICHIAS Saniclean™ gasket and its use in screw coupling connection
Read moreNICHIAS Saniclean™ gasket and its use in triclamp connection
Read more